MILITARY ∙ MEDICAL ∙ AEROSPACE ∙ ELECTRONICS ∙ SEMICONDUCTOR ∙ CONSTRUCTION
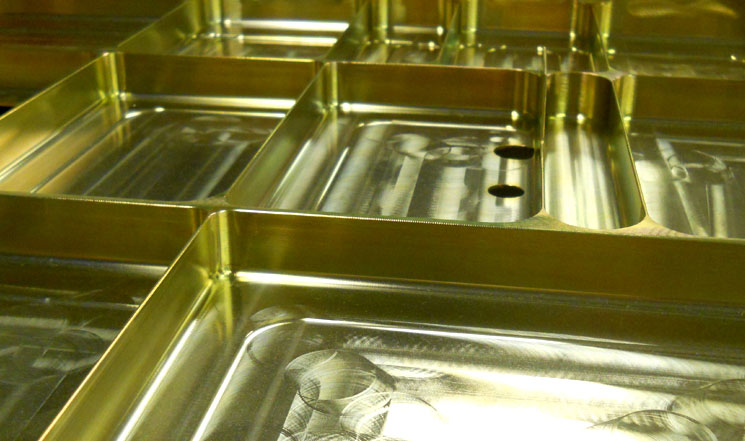
Dry film lubricants are solid materials applied to surfaces to reduce friction, prevent wear, and provide corrosion protection without the need for a liquid lubricant. They work by forming a thin, dry coating on the surface of a material, which minimizes direct contact between moving parts.
Key Features:
- Dry Application: No oils or greases are used, making them clean and less prone to contamination.
- Temperature Resistance: Effective in extreme temperatures where traditional lubricants might fail.
- Long-Lasting: Provides durable lubrication in environments where reapplication is difficult.
- Thin Coating: Ideal for precision parts where space is limited.
Common Materials Used:
- Molybdenum Disulfide (MoS₂): Excellent for high-pressure applications and extreme temperatures.
- Graphite: Works well in high-temperature and low-humidity environments.
- PTFE (Teflon): Offers a low coefficient of friction and good chemical resistance.
- Boron Nitride: Provides thermal stability and electrical insulation.
Applications:
- Automotive: Used in engine components, bearings, and gears.
- Aerospace: Applied to parts subjected to extreme conditions.
- Industrial Machinery: Ideal for components that require clean, long-lasting lubrication.
- Medical Devices: Ensures smooth operation of precision equipment.
Advantages:
- Minimal maintenance.
- Effective under extreme conditions (temperature, pressure, vacuum).
- Cleaner operation compared to liquid lubricants.
- Suitable for complex geometries and hard-to-reach surfaces.
Disadvantages:
- Requires specialized application methods (e.g., spraying, dipping, or curing).
- Initial cost might be higher than traditional lubricants.
- Limited to specific environments and cannot carry away heat like liquid lubricants.
Dry film lubricants are a practical choice for applications where reliability and cleanliness are paramount.