MILITARY ∙ MEDICAL ∙ AEROSPACE ∙ ELECTRONICS ∙ SEMICONDUCTOR ∙ CONSTRUCTION
SANDBLASTING SERVICES IN PHOENIX, AZ
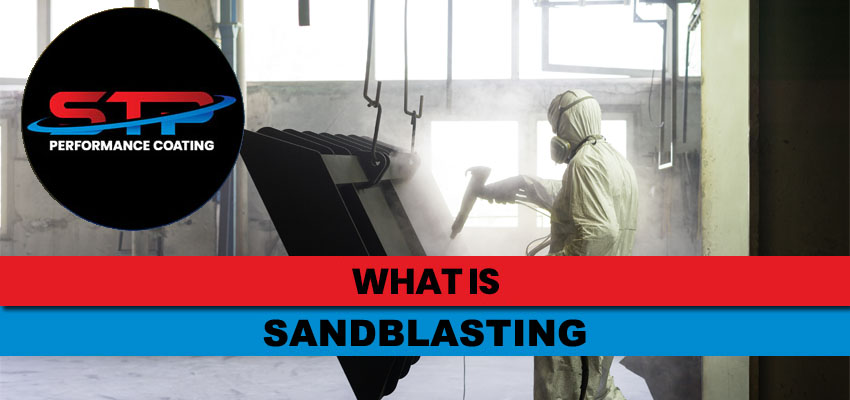
Sandblasting, also known as abrasive blasting, is a process used to clean, smooth, or shape surfaces using high-pressure air or water mixed with abrasive materials. Here are some pros and cons of sandblasting:
Pros:
- Effective Cleaning: Sandblasting is highly effective at removing rust, paint, scale, and other surface contaminants from a variety of materials, including metal, wood, concrete, and stone.
- Versatility: Sandblasting can be used on a wide range of surfaces and materials, making it a versatile cleaning and surface preparation method.
- Precision: Sandblasting allows for precise control over the blasting process, making it suitable for intricate detailing and delicate surfaces.
- Speed: Sandblasting can remove surface contaminants quickly and efficiently, saving time compared to manual cleaning methods.
- Prepares Surfaces for Coating: Sandblasting creates a clean, rough surface that improves adhesion for paint, coatings, and other finishes.
- Environmentally Friendly: Sandblasting is an environmentally friendly cleaning method when using eco-friendly abrasives and containment systems to capture and recycle abrasive materials.
Cons:
- Health Risks: Sandblasting can generate hazardous dust and fumes, posing health risks to operators if proper safety precautions, such as personal protective equipment (PPE) and ventilation systems, are not used.
- Surface Damage: Improper use of sandblasting equipment or abrasive materials can cause surface damage, such as pitting, scratching, or warping, particularly on delicate materials.
- Environmental Impact: Sandblasting can create airborne dust and debris, leading to environmental pollution if not properly contained and controlled.
- Abrasive Material Disposal: Disposing of used abrasive materials can be costly and environmentally challenging, especially if the abrasives contain hazardous substances.
- Equipment Cost: Sandblasting equipment and abrasive materials can be expensive to purchase and maintain, particularly for large-scale or industrial applications.
- Surface Profile Control: Achieving the desired surface profile and finish may require experimentation and skill, as excessive blasting can result in over-etching or roughening of the surface.
- Noise: Sandblasting generates noise levels that may exceed safe limits, requiring hearing protection for operators and bystanders.
Overall, while sandblasting offers numerous benefits for surface preparation and cleaning, it also carries inherent risks and considerations that must be addressed to ensure safe and effective operation. Proper training, equipment maintenance, and adherence to safety protocols are essential for minimizing hazards and achieving optimal results.
How Sandblasting Is Performed
The primary step in carrying out sandblasting is the pouring of sand into the sandblasting machine. These machines have chambers on their top in which the sand gets poured. The sandblasting machine then gets connected to a traditional air compressor that, when turned on, forces the sand out through a hand-held nozzle. Subject to the settings, the pressurization of the sand could be anywhere from 50 PSI to 130 PSI.
Following that sand is “blasted” across the surface, and because of its abrasive characteristics, the sand is capable of creating a smooth surface. Concrete, for instance, is typically sandblasted, to either clean it or preparing it for something. Following the concrete being poured and allowed to harden, it’s then sandblasted. This process removes portions of the excess material on the concrete, as a result making it smooth.
STP PERFORMANCE COATING
STP Performance Coating understands the many benefits of sand blasting. We provide the best sand blasting services throughout the Phoenix Metropolitan area in Arizona including: Phoenix, Glendale, Tempe, Scottsdale, Laveen and more.